O que é um Medidor de Pressão?
Por Gustavo Marinho, CFPHS
Um Medidor de Pressão (ou manômetro) é um dispositivo de medição da pressão exercida por um fluido. Os medidores de pressão são necessários para a identificação e ajuste da pressão nas máquinas e equipamentos que utilizam energia hidráulica, além de serem indispensáveis na solução de falhas operacionais dos equipamentos.
Sem medidores de pressão, os sistemas de energia hidráulica seriam imprevisíveis e não confiáveis. Os medidores ajudam identificar e assim garantir que não haja vazamentos ou mudanças de pressão que possam afetar a condição de operação do sistema hidráulico.
Os sistemas hidráulicos são projetados para trabalhar em uma faixa de pressão definida, de modo que o medidor deve ser classificado para essa faixa. Os medidores de pressão hidráulica estão disponíveis para medir até 10.000 psi, embora as pressões operacionais mais comuns estejam na faixa de 3.000 a 5.000 psi.
Os medidores hidráulicos são frequentemente instalados no pórtico de pressão da bomba ou perto dela para indicação da pressão do sistema, mas podem ser instalados em qualquer lugar onde a pressão precisa ser monitorada – especialmente se sub-circuitos operarem a uma taxa de pressão diferente da pressão da bomba, como por exemplo, após uma válvula redutora de pressão. Muitas vezes, as válvulas redutoras de pressão têm um pórtico de medição para permitir a monitoração direta de sua pressão a jusante.
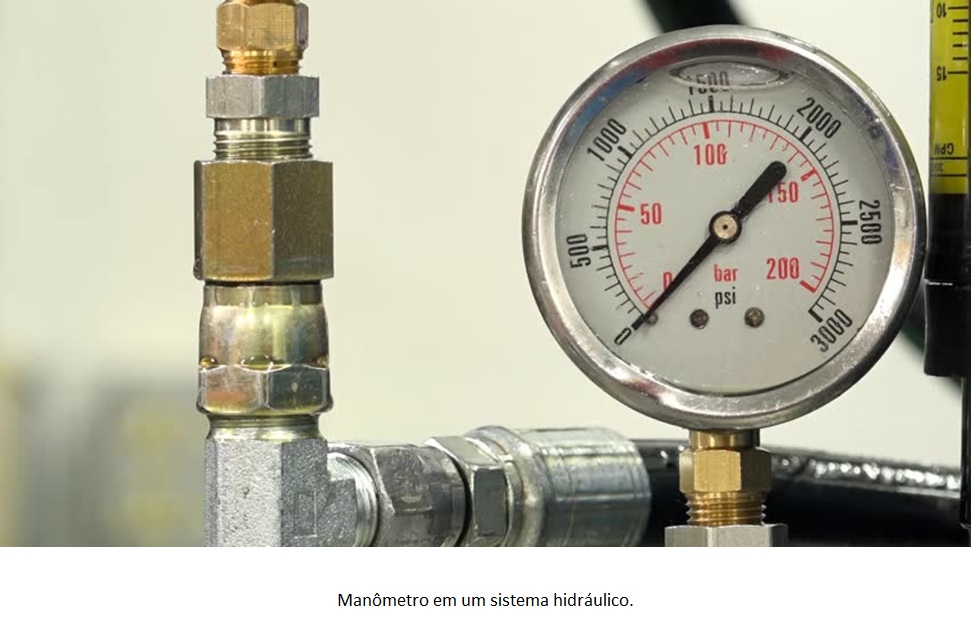
Manômetros de pressão têm sido usados em sistemas hidráulicos por mais de cem anos, então pode ser uma surpresa que os projetos de manômetro continuem a evoluir. A evolução dos manômetros para aplicações de energia hidráulica e pneumática tem sido geralmente, um aumento em recursos específicos de aplicações.
Por exemplo, os manômetros são agora rotineiramente projetados com conexões hidráulicas de pressão (como roscas retas SAE / Métricas) para evitar vazamentos no sistema. Medidores analógicos com escalas personalizadas são mais comuns e medidores de
pressão digitais com firmware personalizável permitem a medição do processo de medição baseada em pressão de vazamentos ou outros parâmetros como torque, carga, força e dureza.
Os sistemas pneumáticos também são repletos de medidores, já que a pressão também é medida em muitos locais em todo o sistema. A pressão é medida no(s) receptor(es), bem como em todos os reguladores FRL ou autônomos do sistema. Às vezes, a pressão também é medida nos atuadores pneumáticos. Normalmente, os manômetros pneumáticos são classificados para não muito mais do que 300 psi, embora os sistemas típicos funcionem em torno de 100 psi.

A pressão é medida de três maneiras – absoluta, manométrica e vácuo. A pressão absoluta é uma medida da pressão real, incluindo o ar ambiente, que é referenciado a zero com um vácuo perfeito, mas pode chegar a 14,7 psi no nível do mar. Leituras de pressão absoluta são consideradas em aplicações que interagem com o ar ambiente, como o cálculo da taxa de compressão para requisitos de fluxo (CFM). A pressão manométrica é referenciada zero em relação à pressão ambiente e é usada na maioria das aplicações que operam no ar ambiente, mas não com o ar ambiente, como em sistemas hidráulicos.
Caso você desconectado do equipamento, um manômetro irá mostrar a pressão como zero. Finalmente, a “pressão” de vácuo é expressa em Torr, ou referenciada em relação à pressão ambiente, como em unidades “in.-Hg” (polegadas de mercúrio), que medem a pressão abaixo da ambiente.
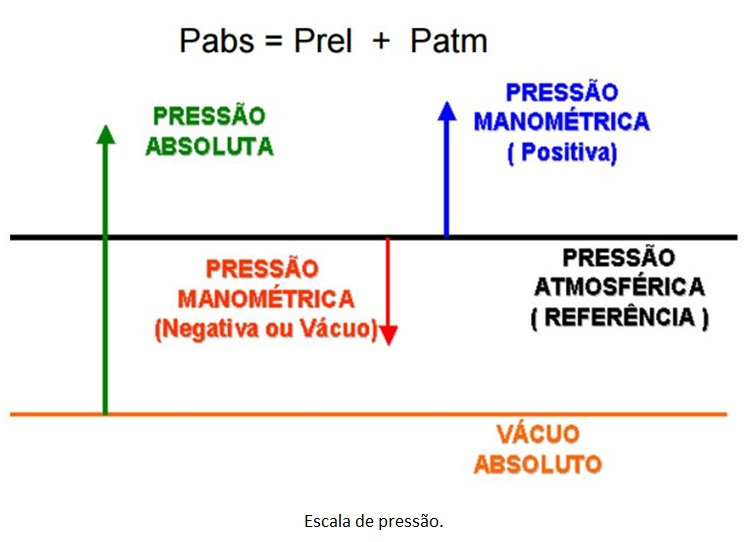
O manômetro hidráulico pode suportar diferentes faixas de pressão com base no tipo de medidor e no material de que é feito. Por causa disso, o tipo de medidor e o material são os critérios de seleção mais importantes para os medidores.
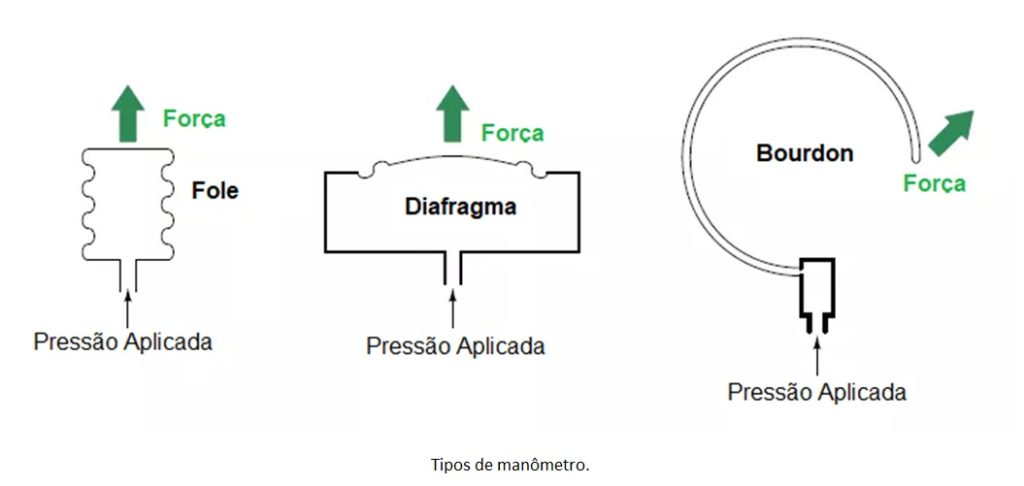
Existem muito tipos de manômetros, sendo os mais comuns o tubo de Bourdon e medidores de fole. Tubo de Bourdon funcionam tomando a pressão e convertendo-a em energia mecânica. Essa energia move um dial no medidor, exibindo a quantidade atual de pressão no sistema. Os medidores de tubo Bourdon são atualmente alguns dos medidores mais comuns e têm diferentes configurações, como curvas, helicoidais e espirais.
O estilo da tubulação, o tamanho do tubo e o material de que é feito variam de acordo com a faixa de pressão. Uma característica importante a ser notada é a mudança na seção transversal tubulação com o aumento da pressão. Geralmente, à medida que a pressão de trabalho do medidor aumenta, a forma da seção transversal do desenho do tubo muda gradualmente de uma forma oval para uma forma circular.
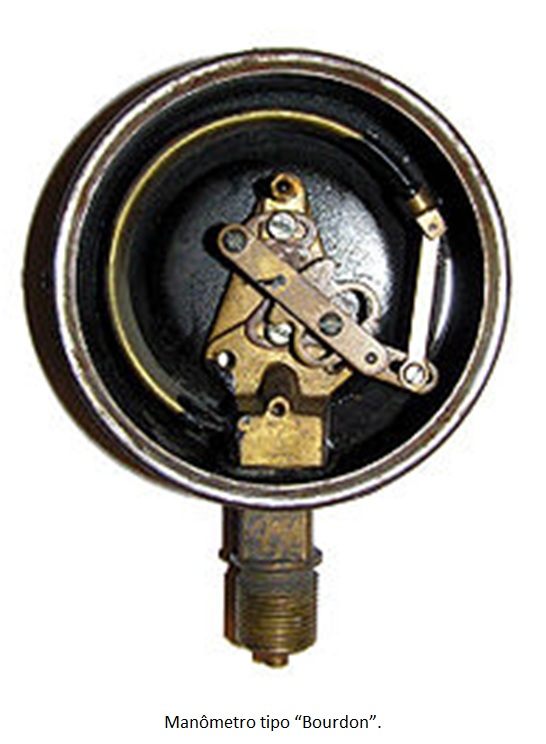
A operação do tubo de Bourdon é simples. Eles consistem em um tubo de metal semicircular e plano, fixado em uma extremidade e ligado a um mecanismo de alavanca sensível na outra. Conforme a pressão aumenta dentro do tubo, a força do fluido tenta esticar o tubo curvo. O tubo então se afasta da alavanca, que está conectada à agulha no visor, mostra a pressão no pórtico do fluido.
Enquanto os medidores de fole funcionam de forma semelhante aos tubos de Bourdon, eles diferem no fato de que eles usam uma mola para medir a quantidade de energia atuando o dial. A mola é expandida e comprimida pela pressão nos tubos e a energia criada por esse movimento é transferida para as engrenagens que movem o disco de pressão.
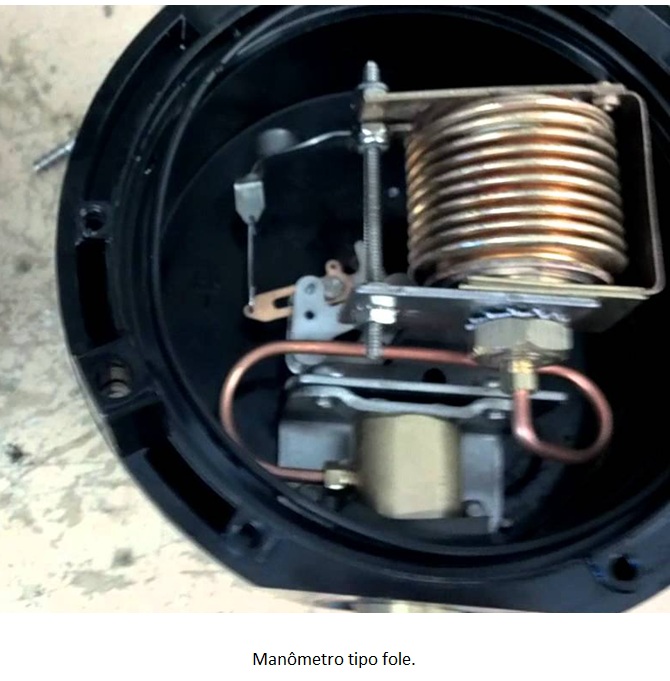
A faixa de pressão na qual o medidor estará funcionando é um fator de seleção principal para o tipo de material usado para fazer o medidor. Medidores que operam em pressões mais altas geralmente tendem a ser feitos de materiais como o aço; quando operando a pressões mais baixas, elas tendem a ser feitas de bronze.
A maioria dos medidores de pressão nos EUA vem com conexão 1⁄4” NPT macho, mas as conexões de rosca tipo SAE vem ganhando popularidade no mercado “Fluid Power”. O uso de adaptadores de ponto de teste em vários locais do sistema hidráulico permite a medição durante a solução de problemas sem a necessidade de comprar dezenas de medidores de pressão. A conexão do ponto de teste é anexada ao medidor, que pode ser parafusado nos pontos de teste em todo o circuito, permitindo que você conecte sob pressão para medir em vários pontos do sistema. A maioria dos medidores tem 2 1/2” de diâmetro e pode ser de montagem superior ou de montagem em painel por clamp ou flange, mas medidores estão disponíveis em diversos tamanhos, materiais e construções imagináveis.
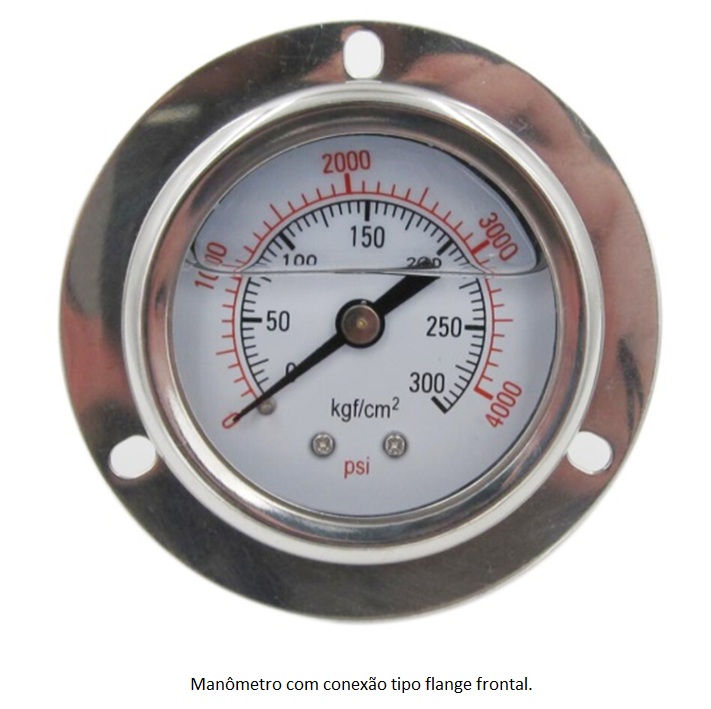

Seja para testar equipamentos ou operar máquinas, os medidores de pressão correto ajudam a reduzir o tempo de inatividade oneroso. Em aplicações de medições mecânicas sistemas hidráulicos, as ameaças comuns para avaliar a confiabilidade são picos de vibração, pulsação e pressão.
Portanto, é melhor procurar medidores projetados especificamente para aplicações hidráulicas. Esses recursos incluem: um invólucro de latão forjado para evitar que as frequências ressonantes destruam os componentes internos; um invólucro cheio de líquido para proteger o manômetro de ciclos de vibração e pressão extrema; e um restritor para evitar danos ao manômetro por picos de pressão. Embora o líquido usado no medidor varie de aplicação para aplicação, a glicerina é comumente usada e tem bom desempenho em muitas condições. Quanto maior a viscosidade do líquido, mais amortece as vibrações.
Ao escolher entre um medidor seco, cheio de água ou glicerina, também é importante considerar o seguinte: faixa de temperatura, tempo de resposta da agulha necessário, mudanças na pressão e a quantidade de vibração esperada da aplicação. Dependendo dos requisitos da aplicação, podem ser necessários acessórios de medição, como restritores especiais, amortecedores de pistão ou até mesmo selos de diafragma, para evitar falha prematura do medidor.
Referências:
– Hydraulic Specialist Study Manual (IFPS)